Reducing Costs and Improving Yields in Infrared Optics
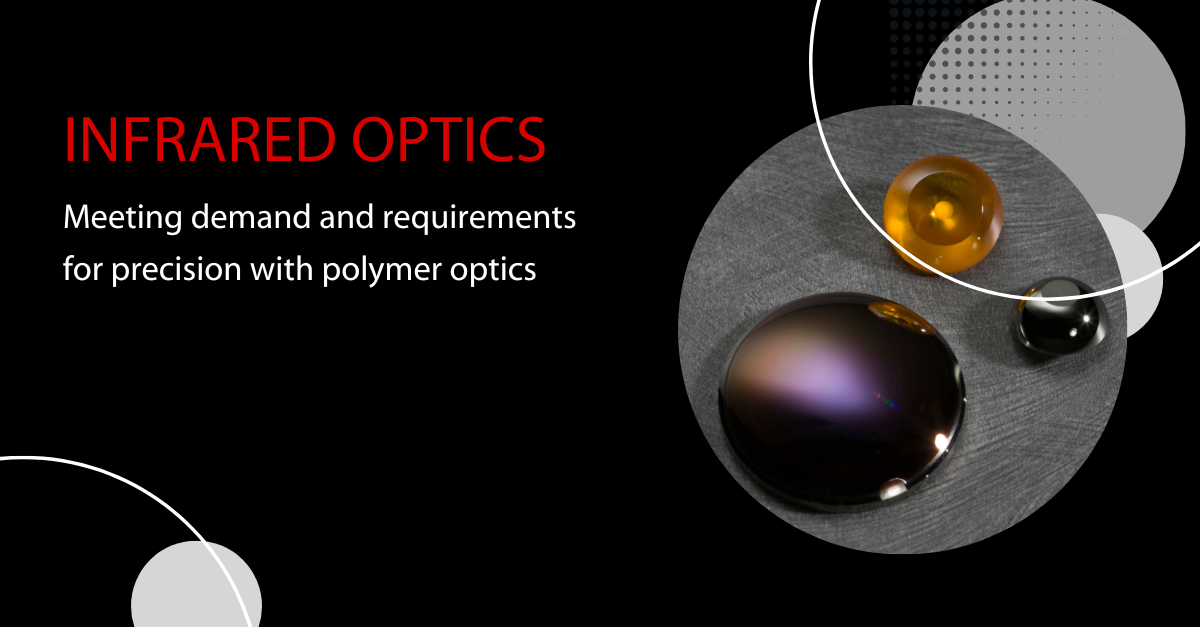
Polymer Optics vs. Chalcogenide Optics in IR Applications
As infrared optics continue to find their way into ever more sophisticated optical systems, optical design approaches must keep pace to meet cost requirements, workforce shortages, supply chain constraints, and demanding performance targets. Traditionally, infrared optics use germanium or chalcogenide glass lenses to deliver crystal-clear images with extreme precision.
Other than military-grade applications or those with the most demanding requirements, many applications simply don’t need the level of precision that germanium and chalcogenides provide—and can benefit from avoiding the high cost, substantial weight, and supply chain risks associated with those materials. Commercial and consumer drones, security and law enforcement systems, and night vision applications can use polymer optics to deliver the right level of precision at a reduced cost, lower weight, and higher yield. This article provides a comparative analysis between injection-molded polymer optics and traditional chalcogenide optics so you can decide which material best fits your optical system.
Materials: Polymer Optics vs. Chalcogenide
Polymer Lenses | Chalcogenides |
|
|
Learn more about FTI’s polymer asphere, PIR, and other injection molded optics capabilities.
Chalcogenide Precision Optics: Renowned for their exceptional optical performance within the infrared spectrum, chalcogenide glass lenses, while superior in quality, tend to incur substantial expenses. The relatively slow and energy-intensive manufacturing processes and optical coating intricacies intensify their cost. Procuring chalcogenide materials and coatings can be a formidable challenge, exacerbating supply chain limitations.
Polymer Optics, Including Fresnel Lenses: Polymer optics, particularly Fresnel lenses, offer a more pragmatic alternative in certain applications to conventional infrared optics. Fresnel lenses excel in cost-efficiency and availability and can stand up to stringent performance requirements, particularly in the ability to capture clear images within the infrared spectrum. Polymer optics also introduce substantial weight savings in Unmanned Aerial Vehicles (UAVs) and handheld portable devices.
Optical Manufacturing Techniques: The Role of Low-Cost Injection Molding
Chalcogenide Manufacturing Complexities: The fabrication of chalcogenide lenses is an intricate, time-intensive process. Traditional lenses designed for the 8 to 14 μm infrared spectrum, such as germanium or zinc selenide lenses, are typically crafted individually, contributing to higher production costs and the need for a highly skilled workforce. Chalcogenide glass lenses are typically molded in a process that requires fabrication of a preform for the molded lens and that requires very large energy input to heat the glass rapidly to high temperatures. The high refractive indices of germanium, zinc selenide, chalcogenide glasses, and similar materials mean that expensive optical coatings are required on every element.
Injection Molding for Polymer Optics: Injection molding offers a transformative approach for the mass production of polymer lenses. This technique offers efficiency, precision, and rapid manufacturing, resulting in lower production expenses and higher yields.
Injection molding can incorporate features for mounting, including flanges and clips, thus simplifying the assembly process. Furthermore, injection molding minimizes the need for highly skilled optics technicians while ensuring consistency and quality in mass production.
Injection molding of polymer optics vs. chalcogenide optics is far less energy-intensive, offering environmental benefits to customers working to comply with ISO 14001.
Applications
Given the increasingly cost-conscious landscape, optical engineers turn to polymer optics for IR applications like:
• Relatively short-range, mid-resolution imaging lenses
• IR windows and domes in combination with standard germanium lenses for environmental protection in applications from UAVs to ground-based camera installations
The injection molding of these cost-effective polymer lenses, crafted from readily available plastic materials, extends the scope of 8 to 14 μm infrared cameras. This expansion includes applications in area surveillance for residential and commercial security, pool safety, continuous industrial process monitoring and maintenance, defect detection, electrical equipment maintenance, night vision for automotive safety, backup cameras, and military and law enforcement applications.
Proprietary IR Materials
Fresnel Technologies offers high-quality polymer lenses for the 8-14 micron region of the IR made from a line of infrared transmitting polymers, the POLY IR® series, each with unique transmittance capabilities. We also offer optics molded from optical-quality acrylic, polycarbonate, cyclic olefin copolymers (COC), and other specialized materials for visible light, near-infrared, and ultraviolet spectra, as well as optics molded from our proprietary POLY IR® 5 material for the 3-4 micron region of the IR.
Explore our offerings:
References:
- Low-cost polymer infrared imaging lens – Richard Claytor & Nelson Claytor, Oct. 10, 2003
- Polymer imaging optics for the thermal infrared – Richard Claytor & Nelson Claytor, Aug. 30, 2004